Residents | A couple visited regularly by their adult children |
Decade of construction | 1790 |
Renovation | 1820, 1931, 1960, 1989, 2007–2008 |
Surface area about | 350 m2 over two floors |
Volume | 850 m3 |
HVAC design | Pohjois-Espoon LVI/Marko Räsänen |
Heating and ventilation solution | Enervent Pelican eco PRO greenair HP and Enervent Pelican eco EDX-E |
Required heating power | 10 kW at –10 °C (additional heat for conditions below –10 °C is provided by fireplaces or direct electrical heating) |
Ventilation cooling power | 9.5 kW |
Ventilation cooling power with dehumidification | 9.5 kW |
Design air flow | 450 l/s |
Comfort of a five-star hotel room in a historic home
Even a house over 200 years of age can be renovated to an energy-efficient condition and improve the quality of indoor climate to the highest level – without compromising on style.
After spending 16 years abroad, this family moved to Askola and bought a farmhouse, which was built in the late 1700s and extended a couple of times. The family familiarized themselves with the possibilities and limitations related to renovation projects for improving the energy efficiency of old houses.
– Trying to make an old house meet the passive house level is not reasonable because its airtightness cannot be improved to the level of a new building. But low-energy levels can surely be met with the help of modern insulation materials and energy-efficient windows, and by utilizing an efficient heat recovery system and heat pumps. When adding thermal insulation layers and sealing up structures, it must absolutely be ensured that these actions do not impair the quality of indoor climate. The correct positioning and careful installation of the vapor barrier must also be ensured, this country gentleman emphasizes.
The old house had natural ventilation that did not work. Heating this two-story, very capacious house in winter was expensive, and due to a sunny hillside location, the indoor temperatures reached the levels of a poor sauna in summer.
The renovation was designed to improve the energy efficiency and comfort of living so that the features that worked well were retained and utilized without compromising the interior style.
Thermal insulation was improved with the most reasonable and ecological method by using cellulose insulation, and the entire roof structure was insulated with polyurethane to save space. The windows of the second floor bedrooms were replaced with new, more energy-efficient windows. The downstairs windows had already been renovated previously.
Constant temperature and high indoor air quality
In terms of comfort of living, the introduction of the mechanical ventilation system was the most essential change.
– Having lived abroad, we were used to a well-functioning mechanical ventilation that can also dehumidify and cool the supply air on hot summer days. That was something we did not want to compromise on.
Marko Räsänen, a highly experienced but now unfortunately deceased HVAC designer, accepted the challenge with the confidence gained from over 500 single-family house design projects. But the solution that was finally selected was a pilot project even for him.
The objective for the ventilation design was a constant indoor temperature of 22 °C and draft-free ventilation regardless of the time of year. Moreover, independent control of a number of rooms was also required. The residents also wanted to keep the old but fully functional tiled stoves operational to provide additional heat. Because the installation of ventilation ducts was inevitable, the most reasonable heat distribution method was air heating – which was rare to find in single-family houses at that time.
When the renovation was planned, the now-adult children lived at home. The consumption of domestic hot water was not very high even for a family of four, and now in a household of two adults it is downright minimal.
– A ground-source or air/water heat pump can be a good solution for a large family. But for us it would have been unnecessary, the owner of the house points out.
A separate system for each wing
The house has two wings, and a separate system was designed for each. If necessary, different indoor air temperatures can be selected for the south and west wings. The air is changed once every hour in one wing, and – thanks to the air recirculation function – at a standard rate of once every two hours in the other wing. One-third of the air is taken from outside, the rest is circulation air.
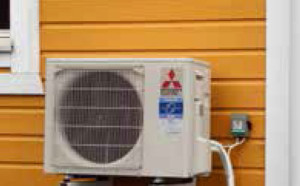
In one wing, ventilation is provided by an Enervent Pelican eco PRO greenair HP, which is a ventilation, air heating and cooling system that is based on a rotating heat exchanger and an integrated extract-air-source heat pump without an outdoor unit. In the other wing, the same tasks are carried out by an Enervent Pelican eco EDX-E equipped with a Mitsubishi outdoor unit. The outdoor unit provides additional power for cooling on the hottest days and for heating at the higher range of sub-zero temperatures. More additional heat can be generated by using the tiled stoves, and the electric heating elements step in at extremely low temperatures.
– But they are not required very often, the owner remarks.
– In total, the two heat pumps provide over 10 kW of heating power with a combined power consumption of less than 4 kW, and they are sufficient for temperatures below –10 °C.
Electric heating is used for additional heating. Electric heaters are located below large windows and set to +17…+18 °C. These prevent uncomfortable cold radiation when sitting in front of the windows during harsh winter frosts.
Plenty of power
The annual efficiency of heat recovery of the Enervent Pelican eco PRO greenair HP is over 90%, and the corresponding value of the Enervent Pelican eco EDX-E is over 70%. The heat pump capacity is not included in the efficiency of the EDX unit. In order to have an air heating and cooling system in a house of this size, the air flow rates had to be higher than what a Pelican unit can deliver. This was why an Enervent Energy MixBox circulation air unit was included in the system. If necessary, it can quadruple the air flow rate, even if the basic ventilation rate is kept constant.
When designing the heating, cooling and ventilation system, the main focus was on energy efficiency. This has proven to be successful: the owner says that at an outdoor temperature of –34 °C, the exhaust air temperature of the greenair HP unit was –28.5 °C with an indoor temperature of +22 °C.
Cooling is also very energy efficient because cold air is recovered as well – or actually warm air is sealed out.
– Even at high outdoor temperatures of +28 °C, the air-source heat pump runs only occasionally, says the pleased owner.
The rotating heat exchangers of the units transfer the heat and moisture from the sauna to the dry indoor air.
– The humidification of indoor air is needed in winter because otherwise the parquet floors and wall paneling in the old house would suffer, the owner explains.
The system does not have a CO2 control function because it is not required if the air flow rates are this high.
Unnoticeable ductwork installation
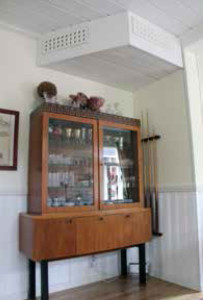
location only.
Many people are hesitant about getting a mechanical ventilation system in an old house because they think that the ductwork installation would be troublesome. In most houses built after the mid-1900s, the ducts can be enclosed so that they should not upset interior designers. If the house is much older, the ducts should be concealed completely, which requires the renewal of interior surfaces. The owner says that he was surprised to see how well Lindab’s pre-insulated ducts could be hidden in a house built in the 1700s. For example, there was just enough space available to install ducts in the slanted ceiling upstairs. The ducts were larger than normal – ø 200 mm, and ø 160 mm for rooms – because they were dimensioned for the higher-than-normal air flow rate required by cooling.
– Sufficiently large ducts also contribute to low ventilation noise levels.
In the kitchen, one cabinet had to be pulled 250 mm away from the wall. The ducts going up to the second floor were concealed with a clever structural solution in the staircase. In fact, the ductwork only needed to be enclosed at one location, and it could have been easily missed if the owner had not pointed it out.
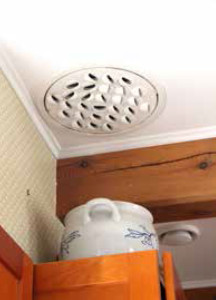
Climecon’s terminal devices, which resemble a flower, blend surprisingly well into the ceiling. A supply air terminal in one bedroom was equipped with a 500-W electric heating element to enable increasing the supply air temperature as quickly as possible.
Naturally, the ducts are carefully insulated to prevent any problems with condensation – and to eliminate efficiency loss.
– Cooling efficiency decreases very rapidly if uninsulated ducts are used, such as under a hot roof.
The actual units were located out of sight in the cellar below the kitchen.
There is always room for improvement
The owner is very pleased with the operation of both systems. However, he is going to improve energy efficiency even further. In the summer, a 2-kW array of panels will be installed on the roof to provide free solar power for the ventilation cooling system and
freezers.
– If I was going to plan a similar renovation project now, I would include a humidity-based control system in the ventilation system and add dedicated combustion air ducts for the tiled stoves, the owner concludes.